Discover the Advantages of Arc Welding in Various Industries
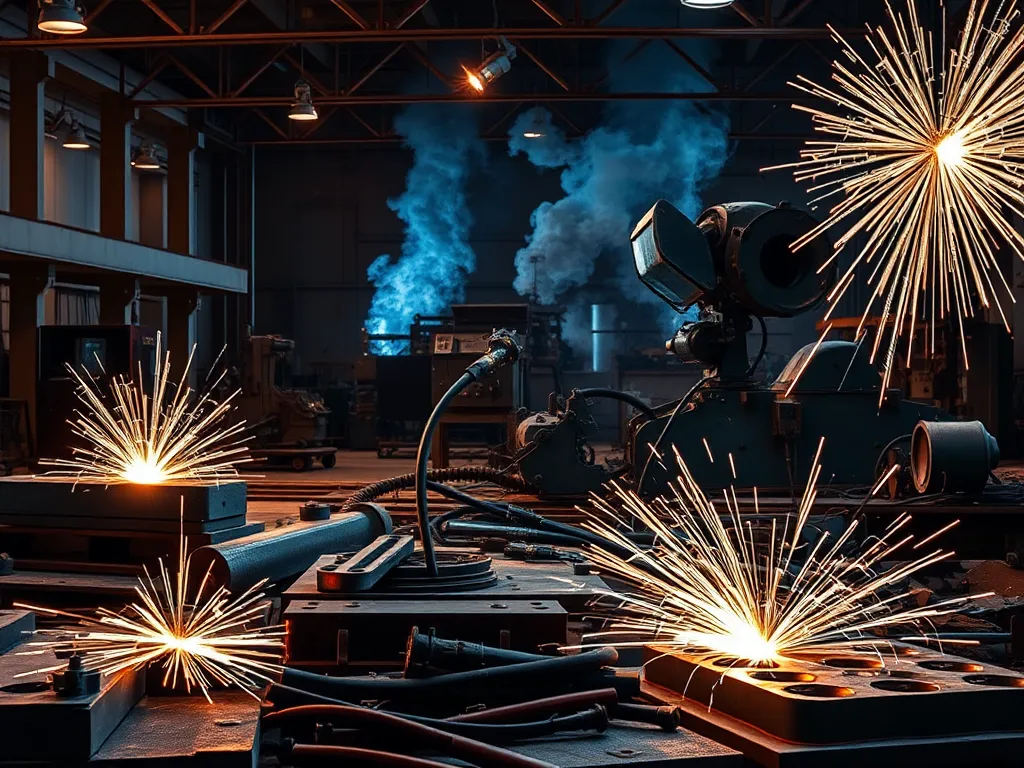
The Comprehensive Guide to Arc Welding
Arc welding is a widely used fabrication process that produces coalescence of materials through the heat generated by an electric arc. The process is notable for its efficiency and versatility, allowing for the joining of various materials and thicknesses. It is employed in numerous industries, from manufacturing to construction, due to its effectiveness and the quality of the welded joints.
Many industries rely on industrial applications to ensure structural integrity and safety in their operations.
The technique of arc welding has evolved significantly over the years, with advancements in technology leading to improved methods and safety practices. It utilizes a consistent electrical current to maintain a controlled arc between an electrode and the workpiece, resulting in intense heat that melts the materials and forms a strong bond upon cooling. This fundamental principle not only enhances productivity but also offers flexibility in applications.
Arc welding is essential in industries where strong, durable joints are critical. It is particularly favored for its ability to weld metals of various compositions and thicknesses, making it a preferred choice in construction, automotive, aerospace, and many other sectors. With the rise of automation, arc welding processes have integrated with robotics, further refining the precision and speed of operations.
The significance of arc welding extends to its environmental considerations, with modern practices focusing on sustainability and waste reduction. With the industry consistently seeking ways to improve efficiency and reduce energy consumption, arc welding stands out as a versatile method that can adapt to these evolving demands.
Enhanced welding efficiency leads to reduced production times, ultimately driving down costs and boosting profitability.
In summary, arc welding is not merely a technique for joining materials; it is a critical component of modern industrial operations. Its adaptability and reliability ensure its continued relevance in a wide array of applications, making it an indispensable skill for welders and engineers alike.
Manufacturing Benefits of Arc Welding
One of the primary manufacturing benefits of arc welding is the increased production speed it provides. The arc welding process allows for quick setup and execution, which can significantly enhance throughput in manufacturing environments, where time is often of the essence. This acceleration in production processes is particularly noticeable in high-volume manufacturing settings.
Cost-effectiveness is another significant advantage of arc welding in large-scale manufacturing. The method minimizes labor and material costs while maximizing output. The ability to create strong bonds with minimal labor input translates to reduced operational expenditures, making arc welding a financially viable option for manufacturers looking to scale their production without incurring excessive costs.
Arc welding also results in improved joint strength, which is a critical factor in manufacturing applications. The welding technique produces high-quality joints that can withstand considerable stress and strain, thereby enhancing the overall integrity of the finished product. This strength is particularly vital in industries such as construction and automotive, where safety and durability are paramount.
The unmatched arc welding versatility allows craftsmen to tackle diverse projects with ease and precision.
The versatility of materials used in arc welding further underscores its benefits for manufacturers. Arc welding can effectively join a wide variety of metals, including steel, aluminum, and titanium, making it suitable for many manufacturing processes. This adaptability allows manufacturers to employ arc welding in diverse applications, from building components to intricate machinery.
Arc Welding in the Automotive Industry
In the automotive industry, arc welding plays a crucial role in car assembly lines. It is used extensively for joining various components, such as chassis, body panels, and structural parts, ensuring that vehicles are assembled with precision and consistency. The automated arc welding machines streamline production, reducing labor costs and minimizing errors associated with manual welding.
Another major benefit of arc welding in the automotive sector is its contribution to vehicle safety. Strong and reliable welds are essential for the structural integrity of automobiles, ensuring that they can withstand impacts and protect passengers. As safety standards continue to evolve, the reliance on arc welding to meet these requirements becomes even more critical.
Innovations in arc welding techniques are significantly impacting the production of electric vehicles (EVs). Advanced methods, such as robotic arc welding, allow for refined control and precision, which is especially important when working with lightweight materials used in EV construction. As the automotive industry pivots towards sustainability, arc welding remains at the forefront of this evolution.
Moreover, arc welding assists in reducing vehicle weight, which is a key factor in enhancing performance and fuel efficiency. By providing strong joints without adding excessive weight, manufacturers can design lighter vehicles that perform better on the road while also consuming less energy, aligning with global sustainability goals.
Construction Applications of Arc Welding
In the construction industry, arc welding is indispensable for achieving structural integrity in buildings and infrastructure. The method is employed to join steel beams, columns, and other critical components, resulting in structures that can withstand heavy loads and environmental stresses. The strength and durability of arc welded joints are unmatched, making them a standard choice for engineers and builders.
The efficiency of arc welding is particularly beneficial in large construction projects. The process allows for rapid assembly and deployment of materials, significantly speeding up construction timelines. In a world where time is money, the ability to quickly and effectively weld components can lead to substantial cost savings and faster project completion.
Compliance with safety standards is another crucial aspect of construction welding. Arc welding provides strong joints that satisfy stringent regulatory requirements, ensuring that structures are safe for public use. Adhering to these safety standards is paramount, and organizations rely on the effectiveness of arc welding to meet these obligations.
Despite its advantages, challenges such as skill gaps and safety hazards persist in construction welding. However, advancements in training programs and safety technologies are addressing these issues, ensuring that the benefits of arc welding can be fully leveraged while minimizing risks to workers and the public.
Arc Welding in Aerospace Engineering
In aerospace engineering, the precision and reliability of arc welding are paramount for manufacturing aircraft parts. The method's ability to produce strong, high-quality welds is essential in ensuring the safety and performance of aircraft, where even minor imperfections can lead to significant consequences.
Arc welding is increasingly used for lightweight materials such as aluminum and composites, which are integral to modern aircraft design. The technology allows engineers to create strong joints in these materials while minimizing weight, which is critical for enhancing fuel efficiency and overall performance.
The impact of arc welding on aircraft safety cannot be overstated. The method produces durable joints that can withstand the extreme conditions encountered during flight. Airworthiness standards necessitate that all welded components meet rigorous testing protocols, and arc welding consistently delivers results that meet these demanding requirements.
Looking to the future, trends indicate that arc welding will continue to evolve in aeronautics, with innovations aimed at improving efficiency, reducing costs, and enhancing sustainability. As the aerospace industry pushes toward more environmentally-friendly designs, arc welding will play a pivotal role in achieving these goals through its versatility and strength.
Environmental Benefits of Arc Welding
The environmental benefits of arc welding are becoming increasingly important in today's manufacturing landscape. The process minimizes waste through efficient welding practices, reducing the amount of scrap material generated during production. This efficiency is particularly vital as industries strive to implement sustainable practices and reduce their ecological footprint.
When compared to other welding methods, arc welding typically consumes less energy, making it a more environmentally-friendly option. With growing concerns about energy consumption and global warming, the shift towards practices that lower overall energy usage is crucial, and arc welding stands out in this regard.
The recyclability of materials welded using arc techniques further enhances the environmental profile of the process. Many materials, such as metals, can be recycled after their useful life, minimizing waste and supporting a circular economy. This recyclability encourages the reuse of materials, further contributing to sustainability.
Lastly, sustainable practices are increasingly being integrated into arc welding operations. Companies are actively seeking methods to reduce emissions and implement cleaner technologies, addressing both environmental impacts and worker safety. As the industry evolves, the focus on sustainable arc welding practices will likely continue to grow, making it a key area of interest for manufacturers and environmentalists alike.