Discover the Key On-Site Welding Benefits for Projects
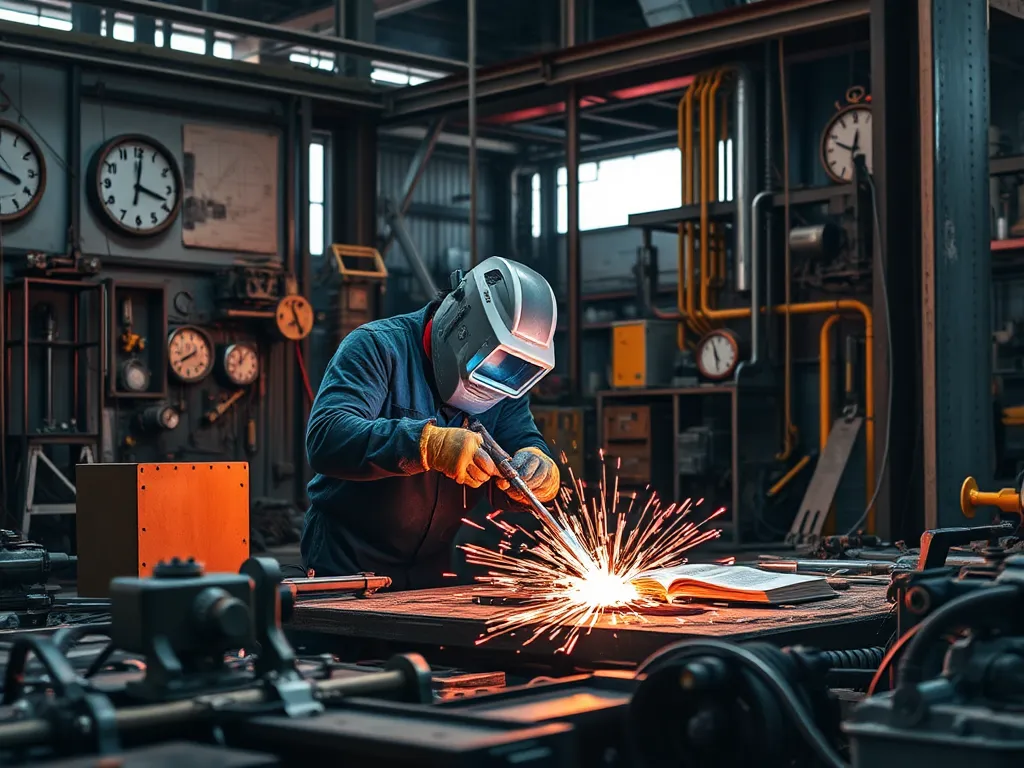
The Advantages of On-Site Welding: Enhancing Efficiency and Quality
On-site welding benefits businesses across various industries by providing immediate solutions without the delays often associated with traditional welding operations. It eliminates the need for transporting materials to fabrication shops, allowing for more efficient project management. This localized approach not only saves time but also enhances overall productivity by permitting quicker presentations of modified designs and immediate workforce adjustments, fulfilling project specifications seamlessly.
Furthermore, the on-site welding process allows for rapid accessibility to skilled welders who can execute tasks within the project locale. This means that project timelines are significantly reduced since there is no waiting period for materials or labor to arrive from distant locations. With minimizing logistical hurdles, the benefits of on-site welding directly translate into more timely job completions, meeting client deadlines without compromising quality.
On-site welding benefits contribute to enhanced flexibility in project execution. By having welding services available at the project site, teams have the opportunity to implement immediate changes and refinements based on project demands. This adaptability is particularly advantageous for complex projects that may require unforeseen modifications, iterating and evolving as work progresses, which is essential in maintaining momentum and achieving desired end results.
Another major advantage is the reduction in labor and transportation costs. On-site welding minimizes the need for multiple trips back and forth between the fabrication shop and the project site, allowing resources to be utilized more effectively. This casts a spotlight on the cost-effectiveness of on-site welding, allowing businesses to allocate their financial resources towards other project needs, potentially improving profit margins while maintaining high-quality work.
Professionals with the right Welding service qualifications are crucial for any project.
In summary, the myriad of on-site welding benefits includes improved efficiency, reduced costs, enhanced flexibility, and streamlined project execution. By integrating on-site welding into their operations, businesses can leverage these advantages to foster growth and success within competitive markets.
Efficiency of On-Site Welding
One of the most significant on-site welding benefits is the reduction of travel time to fabrication shops. By having welding services directly available at the site, teams can begin work almost instantly, cutting out transit delays and enabling them to focus on the task at hand more efficiently.
Moreover, on-site welding allows for immediate on-site adjustments and modifications. When unforeseen issues arise or client specifications change, welders can adapt their work in real-time, leading to a smoother workflow and fewer complications.
Addressing Project-specific welding needs is essential for project success.
The acceleration of project completion timelines is another key factor, as on-site welding eliminates many delays that typically arise from coordinating between multiple locations. This ensures projects remain on schedule and can even lead to earlier-than-expected completions, which can be valuable for client satisfaction.
For those in the market, Mobile welder selection can be a daunting task.
Minimized downtime for projects is an additional efficiency benefit of on-site welding. Since all operations take place within the project area, workers remain engaged without lengthy waits, especially useful in industries where time is of the essence.
Cost-Effectiveness of On-Site Welding
On-site welding also brings notable cost savings, particularly through lower transportation costs for materials. With welding services performed directly on-site, businesses can significantly cut expenses related to transporting heavy materials or tools that often involve logistical challenges.
Additionally, labor costs on-site can be reduced. With teams working in a localized area, the need for multiple workforces diminishes, streamlining compensation structures that can further enhance project profitability.
There is also a minimization of waste, as on-site welding allows for precise welding applications tailored specifically to the project. This degree of accuracy ensures that excess materials are minimized, translating to cost savings over time through efficient resource use.
Potential savings through bulk material use are another consideration. By sourcing materials in larger quantities for on-site projects, businesses can leverage discounts and optimize their procurement processes, contributing to overall cost efficiency.
Quality Assurance in On-Site Welding
Quality assurance is a significant pillar of on-site welding benefits. With direct oversight by experienced welders present at the job site, ensuring quality standards are upheld becomes significantly easier, fostering a culture focused on excellence in workmanship.
Moreover, real-time quality checks during the welding process further enhance project integrity. This feature guarantees that any issues are addressed on-the-spot, preventing potential complications that could arise from incomplete or incorrect welding.
Increased control over environmental factors is another advantage. On-site welding allows for a tailored approach to environmental conditions, ensuring that factors such as temperature and humidity are adequately managed, reducing the risk of defects.
The opportunity for immediate repairs if issues arise is vital, as it directly affects the overall quality of the work being performed. Swift intervention minimizes setbacks and keeps the project on track without compromising quality.
Safety Benefits of On-Site Welding
Safety benefits are pivotal when considering on-site welding. Working in a familiar environment presents fewer hazards compared to transportation and work at distant locations, contributing to safer working conditions for all team members.
Furthermore, there is a reduced risk associated with transporting materials. On-site execution means that heavy and potentially dangerous materials do not need to be moved multiple times, lowering the chances of workplace accidents.
Additionally, the implementation of localized safety protocols can be greatly beneficial. Tailoring safety measures to fit the specific project site ensures that safety procedures are relevant and effective, promoting a culture of safety awareness.
Most importantly, the ability to address safety issues promptly is essential. With teams on-site, any hazards or unsafe conditions can be identified and corrected immediately, enhancing overall safety standards during the project lifecycle.
Innovative Technologies in On-Site Welding
The innovations in on-site welding technologies also contribute greatly to its benefits. The use of portable welding equipment makes it easier to perform complex welding tasks at various locations without the need for extensive setup, expediting processes significantly.
Moreover, the integration of automated welding technologies represents a quantum leap in efficiency and precision. Automated systems can enhance quality and reduce human error, fostering better outcomes for on-site welding projects.
Real-time data analysis and tracking are additional innovations that elevate the onsite welding experience, allowing for precise monitoring of welding operations, performance metrics, and job progress. This technological integration ensures utmost quality assurance while minimizing delays.
Lastly, the advanced welding techniques developed for diverse projects enable welders to tackle a wider range of materials and structures. This versatility broadens the scope of projects that can be effectively managed on-site, reaffirming the strategic advantages of on-site welding.